CMOS Sensor UV Curing

CMOS Image Sensor Application
When the global technology trends engage to Artificial Intelligence and the Internet of Things, the application of CMOS Image Sensors has been extended from traditional camera market such as digital cameras and smart phone lenses to innovative fields such as image recognition, biometrics system and 3D stereoscopic imaging etc. CMOS Image Sensors are also widely applied to high value-added industries such as automotive, security, and medical.
Among these industries, automotive industry is the most potential market to CMOS Image Sensor because The development of driverless and self-driving vehicles is expected to increase the proportion of CMOS Image Sensors used in the automotive industry in the future.
In order to adapt to the harsh environment while car driving, for example, dust, moisture and different climates, the core sensor of the CMOS Image Sensor needs to be packaged and protected by glass. UV glue which features excellent weather resistance, high adhesion strength and anti-yellowing is the most suitable adhesive in the packaging process. However, in the high energy required UV curing process, UV glue tends to inflate and deteriorate due to the 70°C or higher temperature emitted by the electrode type UV light bulbs, and it will result in defective products of the CMOS Image Sensor.
In the UV curing process, conventional electrode UV curing equipment needs to reduce the production speed because of its low energy, and leads to a reduction in productivity. In addition, the waste heat generated by the electrode light bulbs, even after water cooling and air-cooling processes, the high temperature is still 65°C to 70 °C, which easily causes the UV glue to inflate and deteriorate. For instance, in a case of Noda's customer, before the conventional electrode equipment were eliminated, the defect rate of CMOS Image Sensor production is about 5%.
Norda SuperCool UV curing system integrate with Nordson CoolWave II microwave UV curing equipment, and has air-cooling system and complete structural design. SuperCool is able to maintain the temperature below 55 °C while UVA energy output reaches 13.5 J/cm2. It can solve the problem of product deficiency caused by the high temperature, and effectively reduce the defect rate from 5% to 1% when producing CMOS Image Sensor.
Recommend
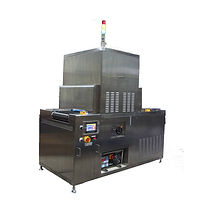
SuperCool UV System

Coolwave UV System
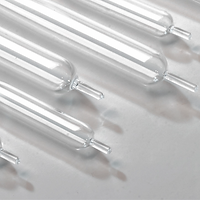