Spin Coating Precision Metering Dispensing Solution

Applications of Spin Coating
Spin coating is a process that utilizes centrifugal force generated by high-speed rotation of a turntable to achieve uniform thickness of the coating on a substrate, resulting in thin and uniform films on smooth surfaces. Common applications of spin coating include the coating of photoresists in the semiconductor, flat panel display, and touch panel industries. It is also used for coating optical films and anode films in lithium batteries.
The advantages of spin coating are its excellent uniformity in coating film thickness and its simplicity of operation. However, its drawback is the significant loss of coating liquid during the spinning process, resulting in low paint utilization. There are many parameters that affect the coating during spin coating, including paint viscosity, solvent evaporation rate, surface tension, and solid content. The precision and stability of the paint application on the substrate during the process can reduce paint waste and achieve uniform coating.
Taking semiconductor photoresist coating as an example, when the amount of coating material is insufficient, the photoresist cannot be evenly distributed on the substrate, which can affect the yield of the product. On the other hand, if the coating is excessive, the excess photoresist will result in increased waste during spinning, leading to low utilization of the photoresist and increased costs. Precise and consistently accurate dispensing of the material is a fundamental requirement for spin coating.
Spin Coating Precision Metering Dispensing Solution
The UBA precision metering pump features extremely high accuracy and repeatable consistency, surpassing a precision level of one in five thousandths. Its unique top-mounted micro-dosing valve design facilitates rapid bubble expulsion and ensures a more stable liquid dispensing volume. It meets demanding requirements in industries that necessitate high precision.
The pump body structure is made of 316 stainless steel, providing excellent corrosion resistance for all components. The diaphragm material options include EPDM, FKM, or Kalrez® perfluoroelastomer, meeting the requirements of various chemical coatings. It is suitable for liquids such as photoresist, electrolytes, chemical fluids, reagents, UV adhesives, inks, gels, and more.
Recommend

UBA E-D Micro Volume

UBA E-C Electric Check Valve
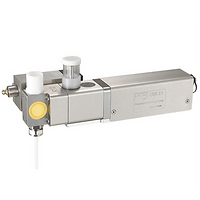