Thermal Grease Coating

Features:
Automated process - Replaces manual attachment of heat sinks, improving process efficiency and accuracy.
Flexible coating size adjustment - The shape and size are no longer limited to pre-cut heat sinks, and can be flexibly adjusted and coated to the desired shape.
Progressive Cavity stator material can be selected - Depending on the temperature resistance, wear resistance, acid and alkali resistance requirements of different coating materials, the most suitable stator material can be selected.
Faster and more accurate than pneumatic needle coating - The pressurized feeding system is equipped with a screw valve for quantitative control, ensuring stable and fast discharge.
Progressive Cavity quantification system - The Progressive Cavity valve is used for quantitative control, overcoming problems such as high metal powder content and viscosity of thermal paste. The discharge accuracy can be maintained within ±1%.
Prevent material sagging - The screw valve controller can control the speed and direction of the progressive cavity valve. When the coating stops, the progressive cavity valve reverses to prevent material sagging.

Dispensing system Specifications:
Pump output ratio: 10:1
Single stroke output volume: 8 ml
Applicable viscosity: 10,000~600,000 cps
Air pressure range: 1~7 bar
Maximum air consumption: 80 ml/min
Power requirements: 220VAC 50/60Hz
Weight: 9.5 kg
Progressive cavity valve specifications:
Dispensing volume: 1 ml/rev
Rotor material: 316 stainless steel
Stator material: NBR, EPDM, Viton, PTFE25%GF, (FDA Grades available)
Output volume: 6~200 ml/min (depending on different materials)
Maximum speed: 200 rpm (depending on different materials)
Operating temperature: can withstand temperatures up to 120℃
Maximum backup pressure: 30 bar
Maximum inlet pressure: 10 bar Weight: 4.8 kg
Recommend
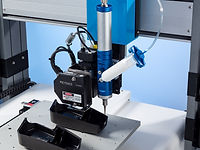
Unilty 4xp Table

1K 797PCP
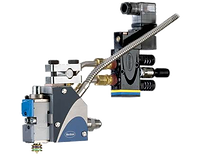